Utilizing Sensor Data for Accurate Predictive Maintenance in Industrial Equipment
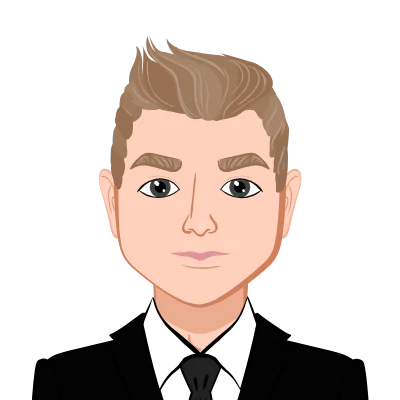
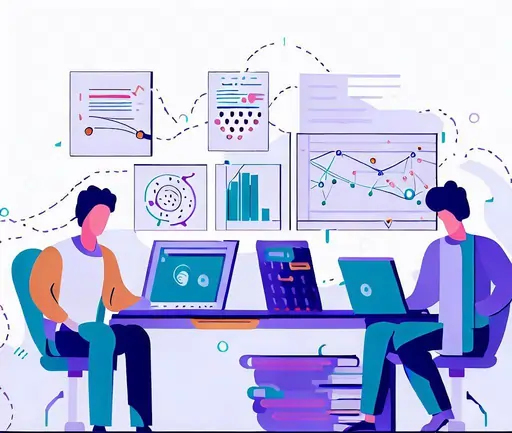
The Importance of Predictive Maintenance
The implementation of predictive maintenance can confer a number of significant benefits on industrial machinery. Organizations are able to proactively identify potential problems and take corrective actions by continuously monitoring sensors and analyzing data. This allows organizations to prevent failures from occurring. This strategy makes it possible to optimize maintenance schedules, which in turn reduces the amount of unplanned downtime and the associated costs. In addition, predictive maintenance boosts operational efficiency by reducing the amount of time spent on manual inspections and other pointless maintenance chores. The utilization of real-time data analysis enables organizations to make educated decisions regarding the health and performance of their equipment, which ultimately results in increased asset dependability and longevity. In addition, predictive maintenance makes it possible to move away from reactive maintenance strategies and towards proactive maintenance strategies. This enables businesses to effectively priorities their resources and maintain uninterrupted operations. In the end, this strategy maximizes the amount of time that equipment is available for use, as well as productivity and the overall performance of the business.
- Detect Anomalies and Faults: The early detection of anomalies and faults in equipment is made possible by predictive maintenance, which in turn makes it possible for proactive maintenance interventions to be taken. When potential problems are identified in advance, businesses have a better chance of avoiding expensive breakdowns and cutting down on downtime.
- Optimize Maintenance Schedules: Predictive maintenance is an approach that optimizes maintenance activities by basing those optimizations on the actual condition of the equipment, as opposed to relying on predetermined schedules for maintenance. This strategy limits the amount of unnecessary maintenance, which in turn lowers costs, while also ensuring that critical components are attended to in a timely manner.
- Extend Equipment Lifespan: It is possible to significantly extend the lifespan of industrial equipment by proactively addressing issues and performing maintenance at the appropriate times. Organizations are able to maximize their return on investment and reduce their capital expenditures if they take precautions to avoid catastrophic failures and breakdowns.
Sensor Data Acquisition and Monitoring
It is absolutely necessary to have access to sensor data that is both accurate and up to date in order to enable predictive maintenance. This information can be gathered with the assistance of a wide variety of sensors, including temperature sensors, pressure sensors, vibration sensors, and many others. Students pursuing master's degrees receive the resources and capabilities necessary to effectively acquire, preprocess, and monitor sensor data through the use of MATLAB Assignment. Students have the ability to interface with sensors, read data, and carry out real-time monitoring by utilizing the built-in functions and libraries available in MATLAB. Students are able to clean and filter sensor data, ensuring that it is of high quality and reliable thanks to the powerful data preprocessing capabilities offered by MATLAB. Students can confidently analyze sensor data by making use of MATLAB's extensive functionality, which enables them to extract meaningful insights and develop predictive models that enable early fault detection and preventive maintenance strategies in industrial equipment.
Data Preprocessing and Feature Extraction
It is necessary to preprocess the sensor data and extract relevant features before applying predictive models. This step comes before the application of predictive models. MATLAB Assignment provides access to an extensive library of functions and methods for the preprocessing of data as well as the extraction of features. Students have the ability to filter noise, normalize data, and eliminate outliers by utilizing the signal processing functions that are available in MATLAB. Students are able to extract meaningful features from sensor data thanks to the numerous algorithms for feature extraction that are provided by MATLAB. Some examples of these algorithms include wavelet analysis, time-domain analysis, and frequency-domain analysis. Students are able to accurately preprocess the data, improve the data's quality, and effectively extract essential features with the help of the robust capabilities offered by MATLAB. These features contribute to the accuracy and effectiveness of predictive maintenance models for industrial equipment.
Predictive Modeling and Analysis
The creation of reliable models that are able to accurately project when pieces of machinery will break down is essential to the practice of predictive maintenance. Students working towards their master's degree gain access to powerful tools for predictive modelling and analysis through the MATLAB Assignment. Students have the option of constructing predictive models utilizing historical sensor data by employing machine learning algorithms such as decision trees, support vector machines, and neural networks. Students are able to evaluate model performance, identify important variables, and fine-tune the models in order to achieve optimal predictive accuracy thanks to the extensive statistical analysis capabilities offered by MATLAB. Students are able to explore different modelling techniques, compare their performance, and select the most appropriate approach to create robust predictive maintenance models for industrial equipment thanks to the user-friendly interface and extensive library of algorithms provided by MATLAB.
Challenges and Considerations
In spite of the many benefits it offers, predictive maintenance does come with a few obstacles. In order to ensure that it is successfully implemented, businesses and students will need to find solutions to these problems. In this context, the quality of the data and its accessibility are two of the most important factors to take into account. Particularly important is the requirement that sensor data be precise, exhaustive, and representative in order to arrive at trustworthy conclusions. In addition, the selection of algorithms and the validation of those algorithms can be challenging for students because they need to understand the benefits and drawbacks of various algorithms before they can choose the algorithms that are best suited for the applications they develop. Organizations and students can optimize predictive maintenance strategies and unlock the full potential of this approach by addressing the challenges that have been outlined above. This will improve the reliability and productivity of industrial equipment.
- Data Quality and Availability: The accuracy and dependability of sensor data is essential to the success of predictive maintenance. Students working on MATLAB assignments for their master's degrees are responsible for ensuring that the data they collect is correct, comprehensive, and accurately represents the conditions under which the equipment is being operated. MATLAB's built-in data preprocessing methods can be used to help address problems with the quality of the data.
- Algorithm Selection and Validation: It can be difficult to select the appropriate predictive modelling algorithms and validate the performance of those algorithms. Students are required to understand the benefits and drawbacks of various algorithms in order to select the algorithms that are the most appropriate for the applications they develop. In order to facilitate and facilitate this process, MATLAB Assignment offers a vast selection of algorithms and validation techniques.
Implementation and Deployment
Implementing and deploying these models is the next crucial step that must be taken after master's degree students have successfully developed and validated their predictive maintenance models using MATLAB. This phase is a prerequisite for moving on to the next step. Students are given the ability to effectively deploy their models into real-time applications thanks to the seamless integration capabilities provided by MATLAB, which are compatible with a wide variety of platforms and technologies. This includes incorporating the predictive maintenance models into industrial control systems, developing web-based dashboards for the purpose of monitoring, or integrating them in a seamless manner into previously established enterprise asset management systems. Students can ensure the practical utilization of their models by taking advantage of the diverse integration options provided by MATLAB. This paves the way for businesses to improve the efficiency of their overall operations and optimize the maintenance of their equipment.
Model Monitoring and Maintenance
Continuous monitoring and upkeep are absolutely necessary if one wishes to guarantee the continued usefulness of predictive maintenance models. Students are given the ability to monitor performance by comparing their predictions with the actual results, which is made possible by MATLAB Assignment's valuable capabilities for model monitoring. This makes it possible to identify any deviations or discrepancies, which in turn makes it easier to make timely adjustments and updates to the models whenever they are necessary. Students working towards their master's degrees can significantly improve the accuracy, reliability, and longevity of their predictive maintenance systems by proactively monitoring model performance and conducting periodic retraining using the tools provided by MATLAB. This iterative approach promotes continuous improvement, ensuring optimal functionality and maximizing the benefits derived from predictive maintenance in industrial settings. It also ensures that there is no waste in the process.
Integration with Internet of Things (IoT)
Because of its capacity to establish seamless connectivity between different types of industrial equipment and data analysis platforms, the Internet of Things (IoT) plays an essential part in the process of making predictive maintenance more accessible to users. Students pursuing master's degrees now have the ability to easily collect real-time sensor data from interconnected devices thanks to MATLAB Assignment's comprehensive support for Internet of Things integration. Students are able to perform advanced analytics on the acquired data by utilizing the capabilities of MATLAB. This allows students to extract valuable insights for the purposes of predictive maintenance. Additionally, the integration enables the automation of maintenance actions based on the results of the analysis, which both optimizes the overall performance of the equipment and reduces the amount of downtime that occurs. The integration of the Internet of Things into MATLAB Assignment broadens the horizons for master's students and gives them the ability to harness the full potential of predictive maintenance in an era when industrial systems are connected.
Conclusion
There is a significant amount of potential for predictive maintenance, which is enabled by sensor data, to significantly improve the functionality and dependability of industrial machinery. Students pursuing master's degrees have access to a powerful tool in the form of MATLAB Assignment, which makes it easier for students to develop and implement advanced predictive maintenance solutions. Students are equipped with the skills necessary to effectively acquire, pre-process, analyze, and deploy sensor data through the use of MATLAB's extensive range of tools and functionalities. This ultimately leads to improvements in industrial processes and fosters operational excellence. Students absolutely need to have a firm understanding of the fundamental principles, carry out careful data analysis, and make use of appropriate models in order for predictive maintenance to be successful. Students have the opportunity to propel their academic pursuits and pave the way for rewarding careers in the field of predictive maintenance if they are able to master MATLAB Assignment. This will give the students a distinct competitive advantage.